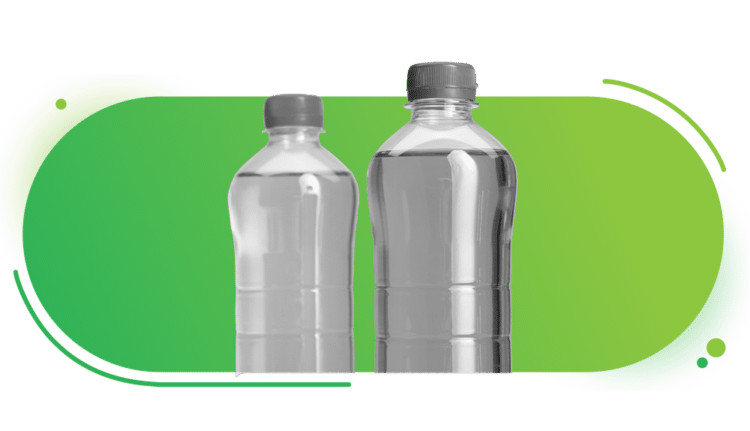
The Opportunity
The customer was experiencing a considerable swing in quality between bottles made during startup and those made during a continuous run. The process was causing numerous starts and stops as a result of line jams and poor label application significantly impacting line efficiencies.
The Innovation
The amount of heat applied before the bottle was blown was adjusted as were the oven settings around start up; including the lamp placement, oven height and opening. The conditions for other process settings were also optimized. The overall bottle quality and consistency between bottles improved.
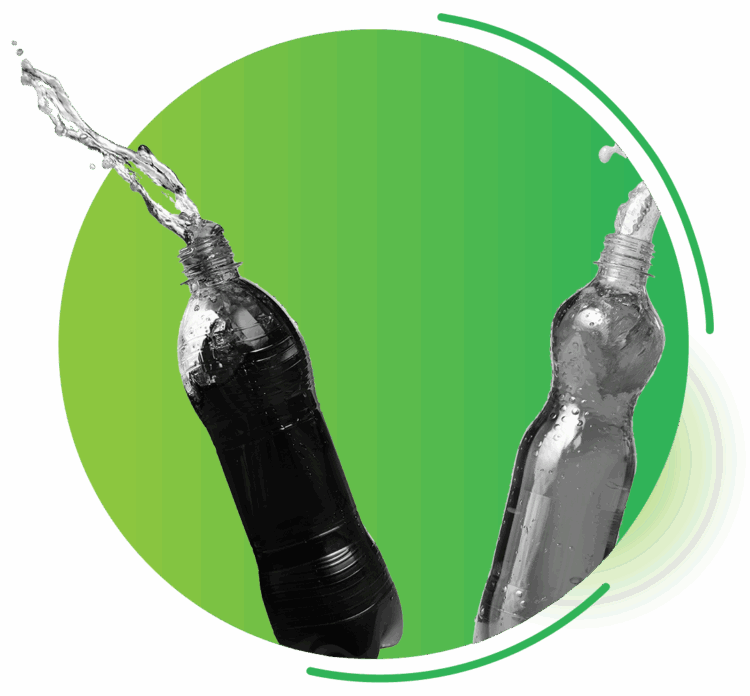
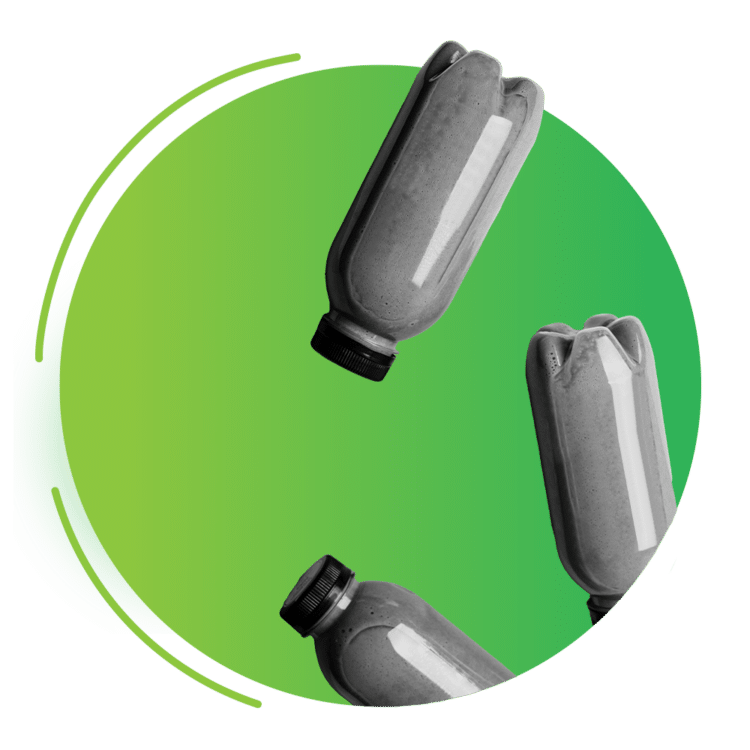
The Outcome
With these changes a large reduction in energy usage was noted as well as an improvement in the overall line efficiencies due to the improved performance and consistency of the bottle.