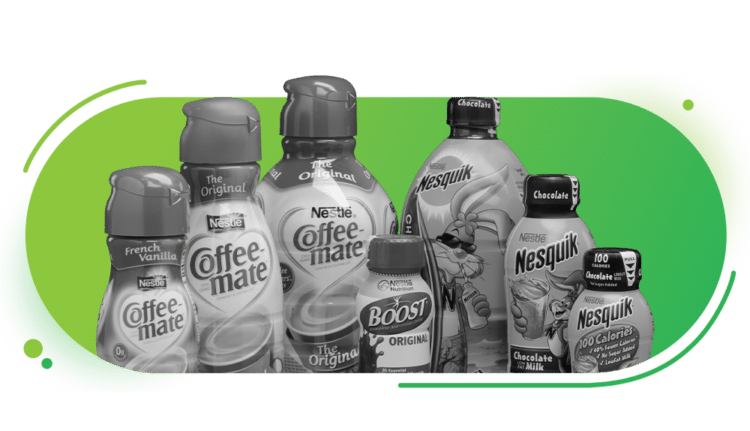
The Opportunity
The customer approached PTI to assist in a packaging transformation to an aseptic filling process to enable the centralization of injection molding, blow molding and filling all under one roof. The objective was to reduce production costs, streamline the supply chain and extend shelf life.
The Innovation
PTI’s initial role was to provide preform and bottle design options. The requirements of the project was that all of the sizes for both product lines required the same size finish and that finish needed to work with different closures and be lightweight in order to reduce production complexity and reduce material usage. PTI worked to adapt the bottle designs and create preforms. Nine different bottle designs (using six preforms) were selected for production testing. Additionally, PTI visited the equipment supplier’s facility in Germany and participated in the onsite acceptance trials for six blow molding and four injection-molding machines.
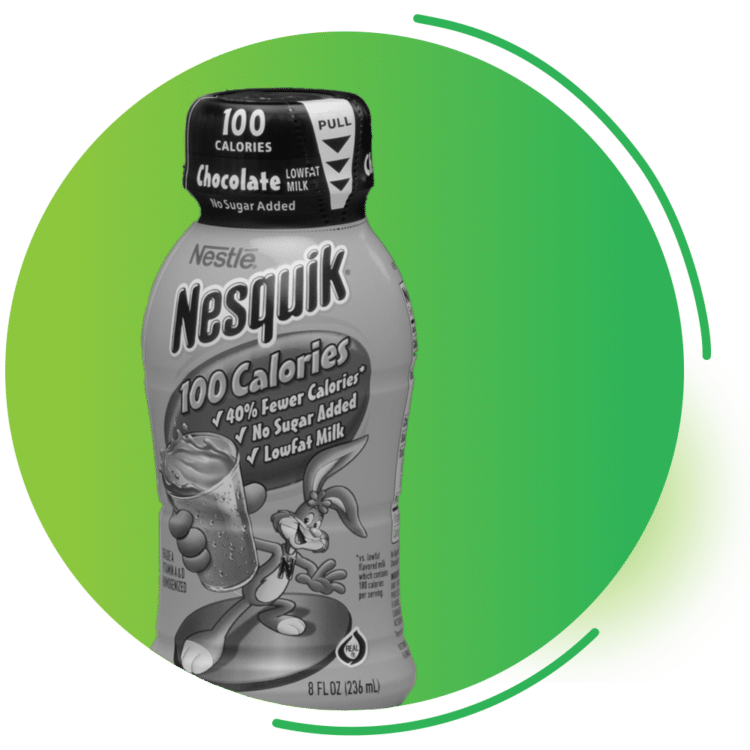
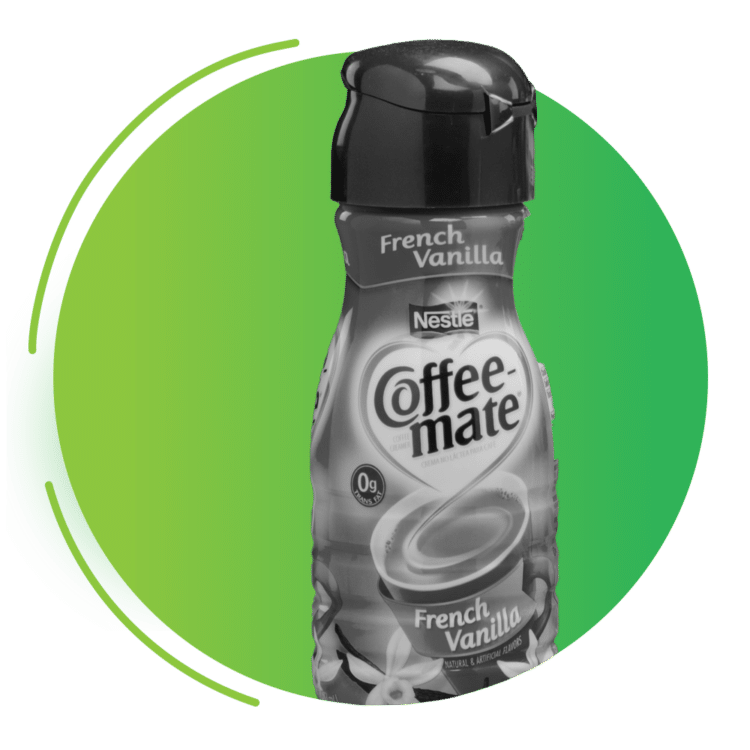
The Outcome
The customer was able to commercialize seven different variations for the two product lines and the new plant is capable of producing over one billion containers per year.